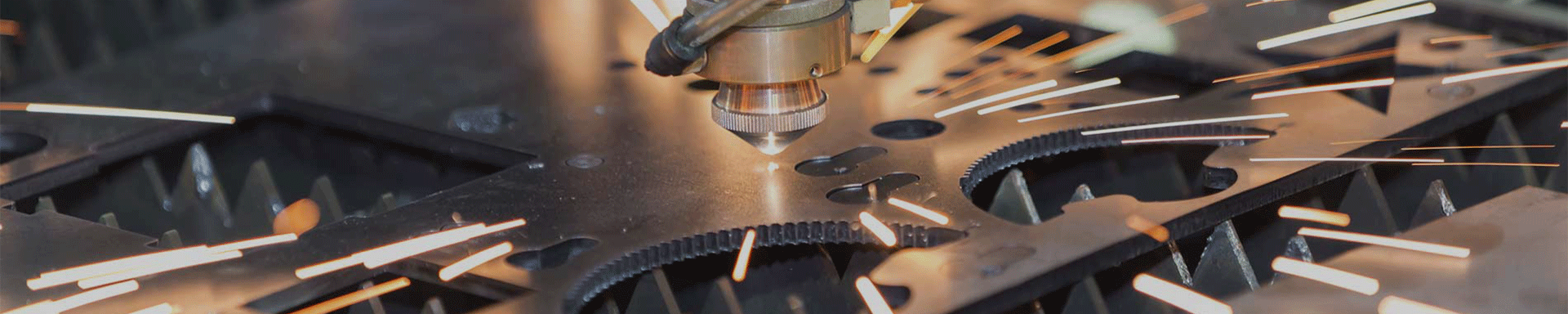
Five main aluminum alloy processing techniques: What are the different methods for aluminum alloy component processing?
2024-07-20 15:37--(Aluminum profile manufacturer + Aluminum profile processing factory.)--
It is well known that a part of traditional manufacturing industries relies heavily on CNC machining. Through computer numerical control systems, CNC machining can produce the necessary components in bulk to meet various project needs. Among these, aluminum alloy is one of the most commonly used materials in traditional manufacturing due to its low density, high strength, and corrosion resistance.
The aluminum alloy component processing can be divided into rough machining and finish machining. After rough machining, the components undergo heat treatment to fully release cutting stress and residual heat. This is followed by finish machining, which significantly improves the quality of the parts.
Let's follow the explanation by our editor at SYHARVEST to learn about the five main aluminum alloy processing techniques and the two main types of aluminum alloy machining.
1. Types of Aluminum Alloy Component Processing Techniques:
Aluminum Alloy Component Processing Techniques:
Using conventional machines such as lathes, mills, planers, drills, and grinders to process mold parts, followed by necessary repairs by machinists, to assemble various molds.
Since mold parts require high precision, using only conventional machines makes it difficult to ensure high processing accuracy. Therefore, precision machines are needed for processing.
To make the processing of punch components, especially complex-shaped punches, die holes, and cavities more automated, and to make the machinist's repair work more automated, CNC machines (such as three-coordinate CNC milling machines, machining centers, CNC grinders, etc.) are required for mold processing.
2. Aluminum Alloy Component Stamping Process:
Stamping is a forming process that relies on a punch press and a die to apply external force to sheets, strips, pipes, and profiles, causing them to undergo plastic deformation or separation to achieve the desired shape and size of the workpiece (stamped parts). Stamped parts are produced by the power of conventional or specialized stamping machines, causing the sheet material to directly deform in the die, resulting in products of specific shapes, sizes, and properties. The three main elements of stamping processing are the sheet material, the die, and the equipment. Stamping is a method of metal cold deformation processing, also known as cold stamping or sheet metal stamping, and is one of the primary methods of metal plastic processing.
3.Aluminum Alloy Component Casting Process:
This process involves precision casting, a type of special casting. The components produced by this method often require no further machining, such as in investment casting and pressure casting. Compared to traditional casting techniques, precision casting is a method that yields more accurate shapes and improves casting precision.
The general procedure is as follows: first, design and manufacture the mold according to product requirements (with very little or no allowance), then cast the original wax model by pouring wax into the mold. Repeatedly coat the wax model to form a hard shell, dissolve the wax model to create the cavity, and then fire the shell to achieve sufficient strength. Finally, pour the metal material into the shell, and after shell removal and sand cleaning, a high-precision finished product is obtained. The product may then undergo heat treatment and cold working as required.
4. Aluminum Alloy Component Powder Metallurgy:
Powder metallurgy is a technique that involves using metal powders (sometimes with the addition of a small amount of non-metal powders) to mix, mold, and sinter metal powders to create materials or products. This process consists of two main parts:
(1) Manufacturing metal powders (including alloy powders, collectively referred to as "metal powders").
(2) Mixing metal powders (sometimes with a small amount of non-metal powders), molding, and sintering them to produce a material (referred to as "powder metallurgy material") or a product (referred to as "powder metallurgy product").
5. Aluminum alloy spare parts injection molding:
The solid powder is evenly mixed with an organic binder, granulated, and then injected into the mold cavity through an injection molding machine in a heated plasticized state (approximately 150℃) to solidify and form. The binder is then removed from the formed blank using chemical or thermal decomposition methods. Subsequently, the product is sintered and densified. Compared to traditional processes, this method offers high precision, uniform structure, excellent performance, and lower production costs. Its products are widely used in industrial fields such as electronic information engineering, biomedical equipment, office equipment, automotive, machinery, hardware, sports equipment, watchmaking, weapons, and aerospace.
2. Aluminum alloy processing methods:
Modern aluminum alloy processing includes semi-finished aluminum alloy processing and finished aluminum alloy processing. So, what are the various methods of aluminum alloy processing?
There are three methods for finished aluminum alloy processing:
1. Extrusion in aluminum alloy processing. We use extrusion in the manufacturing of molds, where the aluminum ingot is compressed through the mold using a press. We process small batches of aluminum alloy using the manufactured molds to meet customer requirements.
2. Straightening in aluminum alloy processing. Straightness in aluminum alloy processing needs to be checked and adjusted using a straightening gauge to meet industry standards and daily demands.
3. Post-oxidation treatment in aluminum alloy processing. After the aluminum alloy passes the inspection, it needs to undergo oxidation treatment before it can be used. This process ensures aesthetic appeal, corrosion resistance, and wear resistance.
3. There are four methods for finished aluminum alloy processing:
1. Cutting in aluminum alloy processing. Typically, the standard length of an aluminum profile is 6.02 meters. However, in actual production, various combinations of aluminum alloy lengths are required. Therefore, it needs to be cut according to specific requirements to ensure the cutting length and precision.
2. Punching in aluminum alloy processing. Industrial aluminum alloy installation usually involves the combination of multiple aluminum profiles and fittings of different specifications. Connection components require pre-embedded holes, which need to be punched according to the design requirements using specialized punching machines.
3. Tapping in aluminum alloy processing. Industrial aluminum profiles, fittings, and connection components often require the use of bolts, nuts, and screws, which need to be tapped.
4. Milling slots in aluminum alloy processing. To facilitate the assembly of other accessories in the later stages, it is often necessary to mill slots on the surface of the aluminum alloy, ensuring the efficient installation of other accessories.
The editor believes that you are already familiar with the various aluminum alloy processing methods and techniques. Aluminum alloy is an essential material for CNC machining in daily production. In addition to selecting CNC machining materials, it is also crucial to choose a CNC machining manufacturer at http://www.syharvest.com .This ensures not only the quality of CNC machining but also a good experience with CNC machining services.