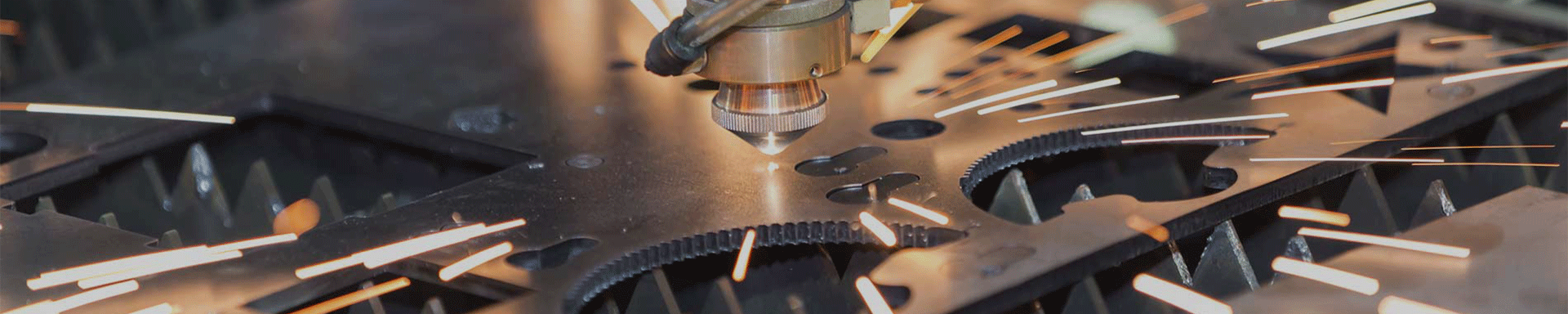
- Home
- >
- Products
- >
- industrial heat sink
- >
industrial heat sink
heat sink is a device used to dissipate heat and is usually used for heat dissipation and temperature control of heat sources in industrial production processes. It has a wide range of applications in various industrial scenarios.
syharvest have the best capability and strength that can Fulfillment of your requirements
Some of the benefits of aluminum CNC machining include:
*High accuracy and repeatability
*Complex part geometries
*Lightweight and strong parts
*Corrosion resistance
*Low cost
- Syharvest
- Foshan
- 15days
- 4000 Ton/Mouth
- Information
| ||
NO. | ITEM | DESCRIPTION |
1 | Material | aluminum |
2 | Dimension L*W*H | up to 1000*1000*1000 mm |
3 | The minimal wall | 2 mm |
4 | Tolerance limit | 0.012 mm |
5 | Surface flatness limit | 0.02 mm |
6 | Surface roughness limit | 2.4 um |
7 | Surface finish | Mill finish or custom finish |
8 | Packing way | With film protection and packed in carton box or plywood case |
9 | Manufacturing Method | Full cnc machining |
10 | Warranty time | 1 year |
11 | Place of Region | Jiangsu province of China |
12 | Reference Standard | GB/T 3190-2008,ISO2768 |
Metalli’s machining capability covers below:
◆ 5 Axis CNC Machining ,CNC Milling ,CNC Turning;
◆ EDM Wire-cutting, WEDM-HS ,WEDM-LS;
◆ Milling, Turning, Grinding.
◆ Surface Treatment
◆ 5 um tolerance precision limit
◆ Length/width/diameter up to 1 meter
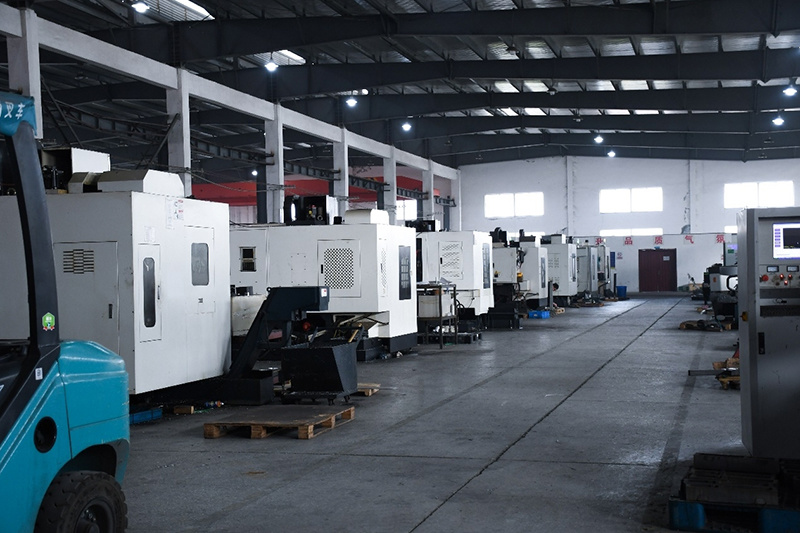
Brief of CNC machining
Computer Numerical Control (CNC) machining is a manufacturing process in which pre-programmed computer software dictates the movement of factory tools and machinery. The process can be used to control a range of complex machinery, from grinders and lathes to mills and CNC routers. With CNC machining, three-dimensional cutting tasks can be accomplished in a single set of prompts.
The CNC process runs in contrast to — and thereby supersedes — the limitations of manual control, where live operators are needed to prompt and guide the commands of machining tools via levers, buttons and wheels. To the onlooker, a CNC system might resemble a regular set of computer components, but the software programs and consoles employed in CNC machining distinguish it from all other forms of computation.
When a CNC system is activated, the desired cuts are programmed into the software and dictated to corresponding tools and machinery, which carry out the dimensional tasks as specified, much like a robot.
In CNC programming, the code generator within the numerical system will often assume mechanisms are flawless, despite the possibility of errors, which is greater whenever a CNC machine is directed to cut in more than one direction simultaneously. The placement of a tool in a numerical control system is outlined by a series of inputs known as the part program.
With a numerical control machine, programs are inputted via punch cards. By contrast, the programs for CNC machines are fed to computers through small keyboards. CNC programming is retained in a computer’s memory. The code itself is written and edited by programmers. Therefore, CNC systems offer far more expansive computational capacity. Best of all, CNC systems are by no means static since newer prompts can be added to pre-existing programs through revised code.
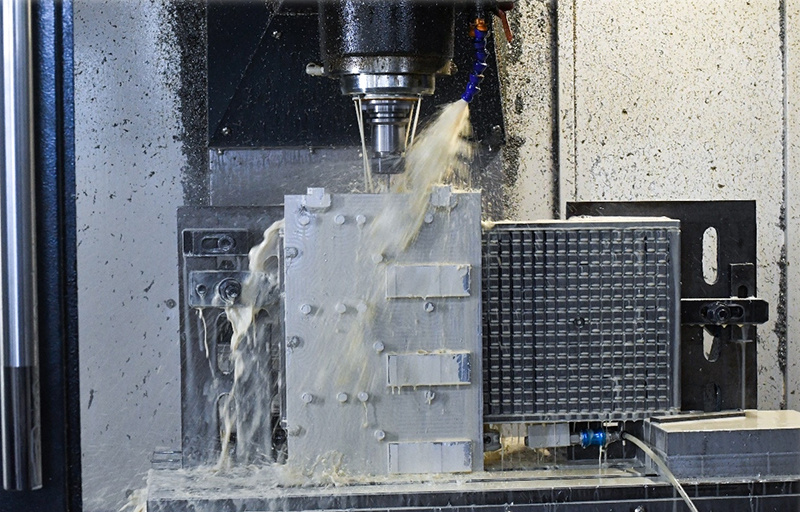
key word: